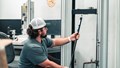
Design World: How to Choose a Safe, Effective Counterbalancing System
Strenuous movements that include heavy lifting, pushing or straining account for most non-fatal workplace injuries across the United States. In fact, 84% of injuries resulting in time away from work are caused by overexertion, reactions (such as slips or falls) or hazardous contact with objects and equipment.
What’s more: employees 45 to 55 are most susceptible to injuries caused by overexertion and workplace accidents. While construction, transport or delivery workers are commonly affected due to the heavy loads that require lifting, these risks are also pervasive in other industries.
Case in point: A lab technician at a medical facility gets her finger caught in a heavy equipment-access door that unexpectedly closes, causing a laceration and possible lab contamination. Or consider an airport’s access panel to underground infrastructure systems. The panel must be heavy enough to withstand airplane weights and accessible enough to open without the use of large and costly lifting equipment.
Now imagine an operator gains underground access with ease, but then the panel fails to hold, locking him underground. In both examples, the safety and reliability of the equipment are at fault, and the solution is a carefully chosen and properly installed counterbalancing system.
The importance of counterbalancing
A counterbalance is a weight or force that offsets or mitigates another weight or force. Typically, counterbalancing systems incorporate springs or struts to effectively support a cover, panel, door or another device. Within these systems, there are mechanical, gas and hydraulic options. The ideal choice depends on the application and the environment it will be subject to.
In the above examples, the ideal counterbalancing solution would reliably support a user in safely accessing the lab’s equipment door or the airport’s underground panel as required without risk of user injury — regardless of the weight of the door or panel.
“Consider that in infrastructure applications, a seemingly simple panel or hatch door might weigh 300 or 400 pounds or more,” shares Steve Rockow, manager, global engineering. “The counterbalancing system used must support a specified mass and hold it open as needed without fear of sudden failure.”
“Many industries also hold specific weight and lifting restrictions for the safety of their workers or employees, so an ideal system is designed to stay below these limitations to adequately meet the restrictions,” adds Jeanne Bogre, senior director of sales. “It’s often necessary to offset certain loads or weights to make it safe for one person to open a panel or door without the assistance of a machine.”
Fortunately, there are options in modern counterbalancing systems. Self-opening mechanisms are one such possibility.
“So, a ground hatch might have a closed latch position, but then when the latch is released, it will open on its own,” says Rockow. “The counterbalance system can also be installed to meet certain speed restrictions, maintain a certain rotation and those types of features.”
Another important feature for many applications is ensuring that once a panel, hatch or door is opened that it locks securely in place.
“If you’re opening a heavy door or underground access panel, it’s critical a worker is not caught, crushed or stuck in a confined space,” he explains. “The panel must positively stay open, regardless of a gust of wind or what have you. So, there are locking mechanisms called Prop-Locks that can be installed as an added safety mechanism.”
Such locks can offer a manual release to ensure the panel only closes when an operator manually disengages it. This allows for the safe, intentional closing of the panel or hatch, ensuring no operator is accidentally locked in an area or harmed when the panel or door closes.
In the above example, the lab’s equipment door is one instance where the counterbalancing system did not remain open long enough to allow safe entry.
Aside from mechanical locking mechanisms, today there are also electromechanical struts that can be electrically installed with a control panel for use with a simple switch.
“There are several options to ensure the best and safest choice, depending on user preference and the requirements of a project,” adds Bogre.
Regardless of the option, choosing an ideal counterbalancing system is a critical decision that should reflect the needs of the workers or operators while meeting the unique features of the application.
Choosing the right system
Each application has its own unique requirements and possible challenges when it comes to choosing and installing the ideal counterbalancing system. The goal is always to reduce the weight of an object (such as a panel, cover or door) and provide the end-user with control and a sense of safety. Ideally, the system also offers longevity, requiring little to no maintenance.
The types of counterbalancing systems include:
1. Mechanical. A seal-less, gas-less and oil-less counterbalance solution that requires no maintenance and typically lasts the lifetime of the application. This choice is ideal in environments subject to corrosion or variable conditions, where failure is not an option. Mechanical struts can produce consistent, repeatable loads at varying intervals. This is the most environmentally friendly option.
2. Gas. Gas Struts consist of a precision rod attached to a piston, moving within a sealed cylinder that contains pressurised nitrogen gas and oil. They provide lift assistance and counterbalance to applications via a push or pull force that acts around a pivot axis.
“These are also referred to as gas shocks, and they’re a viable solution when the environmental temperature is stable. Because they’re closed, pressurised devices, this pressure can change in hot weather, for instance, and that changes the force output,” explains Rockow. “Corrosion can also be a concern, but stainless-steel versions are available, so there are solutions to mitigate certain conditions.”
It’s also worth noting that gas springs have seals that protect the oil inside, but these seals wear over time, so maintenance is typically required.
3. Hydraulic. Hydraulic systems function and perform tasks using pressurised fluid. Counterbalancing systems can provide an efficient alternative to conventional hydraulic pumps or high-pressure hoses, which can be costly and problematic.
“The mining industry comes to mind as an example of a hydraulic system,” says Rockow. “It often uses huge gravel haulers with tyres that are 16 to 20 feet tall and have massive buckets at the back for the gravel. These trucks typically have large access panels where an electromechanical strut is ideal and far more cost-effective than a hydraulic pump that requires fluid and cylinders to actuate. This electromechanical strut system uses low direct-current voltage instead.”
Asking the right questions
“There are several questions to ask before choosing a counterbalancing system,” adds Rockow. “There’s the mass to consider, the centre of gravity, the possible mounting locations of the struts or springs, the conditions the application will be subject to, and flexibility we have within these factors. This will all vary per customer and application.”
Another important consideration: The longevity of the application. How long must the product work and how often is its counterbalance system in use? Is it only every few months (such as an access hatch for maintenance of underground pipes or infrastructure), once or twice a day (such as for a food truck door), or once or twice an hour (like for heavy equipment)?
“Aside from calculating the cycles, the product is expected to make every day, week or year, it’s important to think about the environment before choosing a counterbalancing system,” says Bogre. “Gas might be out of the question if the application is underground, or variable weather is a concern. Or maybe a preferred hydraulic system requires a hydraulic source — but the application must be self-contained, so this option is off the table. Asking the right questions will help with choosing the right system.”
To properly assess these factors, a host of technical information is required. To simplify the process, ASRaymond offers a free, online Counterbalance Configuration Tool.
“This tool takes the complicated engineering equations and provides options. It’s simple and efficient to use, so an engineer can type in the parameters of the specific application, and it determines a few of the best counterbalancing options,” she says.
This includes the application’s variables (such as the angle, depth and height), the load and strut specifications, essentially taking any guesswork out of the equation.
“This tool also solves the trial-and-error approach so someone can avoid buying five or six springs to try and test, just hoping one of the options works out,” adds Rockow. “That gets costly because you must buy the components, figure out the different mounting options, drill holes, add brackets if needed, and potentially move things around and try a different component.”
The Counterbalance Configuration Tool calculates the results and typically offers five or six strut or spring options, including the best mounting points and handle loads for the project in question.
In summary, when choosing a counterbalancing system, consider:
- The mass or rotational mass
- The centre of gravity
- Flexibility and possible mounting locations of the struts
- Environment
- Ergonomics
- Maintenance considerations (such as easy access for cleaning, particularly for industries that have strong hygiene requirements like the medical sector)
- Any other preferences or restrictions
Ensuring accessibility
“Today, the average worker looks different today than 50 years ago,” says Bogre. “In many fields, there’s an ageing workforce. There are also a lot more women in almost every industry. It’s important to be more inclusive and safety conscious when it comes to equipment designs and ergonomics.”
In terms of a counterbalancing system, this means choosing a system and designing an application that’s accessible to every type of worker who might use it. This might involve a decision to reduce the additional mass of an access panel for easier entry or it could mean installing an electrical control system actuated by a switch to ensure an employee never risks injury.
Ideally, such choices are made at the design stage of an application.
“Too often, counterbalancing systems are considered at the end stage of product design, which is far from ideal,” says Rockow. “In such cases, you’re potentially limiting your choices and adding time and costs to the final application.”
“To put this in perspective, considering the counterbalancing solution early in the design cycles allows more leverage,” adds Bogre. “For instance, if an application is already designed and there’s only a small mounting space available to install the struts, there’s little leverage to work with. You might need large struts to work effectively, but there’s not enough mounting space to properly accommodate the requirements. It’s very important to kind of think of this earlier rather than later.”
For this reason, it’s important to consider the lift and handle loads necessary for an ideal counterbalancing system as early as possible in an application’s design to ensure the best and most cost-effective solution.
“We’re typically able to recommend or develop a solution to any counterbalancing requirements, but you give yourself with more options — and often standard instead of more costly customised ones — the earlier in the process this is planned for,” says Rockow. “Counterbalancing should be an important early decision for safety and leverage reasons and, when possible, not something that’s left to the end of a project’s design cycle.”
Along with the Counterbalance Configuration Tool, ASRaymond offers the online option to design a counterbalancing solution into a product or application.
“This allows engineers the opportunity to visualise the final design, consider different options and order parts or prototypes directly online, simplifying the entire process,” says “They can choose the most important features, such as including a locking mechanism or what have you for added safety. We always want to ensure customers have and understand the best options available to ensure the safest, most effective counterbalancing system for their application.”