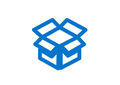
Material Creep: Reduce Spring Stress
When creep and fatigue start to set in, the life cycle and performance of the spring can be negatively impacted, which can, in turn, impact the application's ability to function as intended. So what is creep?
Material Creep: Reduce Spring Stress
Springs are used in a variety of applications and operations. Often, springs are the last component to be considered and designed into an application, but that does not make them a non-critical aspect of the machine. Springs will experience wear and fatigue over time, even if they are not attached to the most active part of the application. When creep and fatigue start to set in, the life cycle and performance of the spring can be negatively impacted, which can, in turn, impact the application's ability to function as intended.
What is Creep?
Creep is an increase in plastic strain under constant stress or load. It is a process that happens over a long period of time and is accelerated as service temperatures increase. It is unique in that it occurs when the stress condition is in the elastic range of the material's stress-strain curve.
Additionally, it is unique because the springs material begins to plastically deform — the permanent distortion that occurs when a material is subjected to stresses that exceed its yield strength — even though yield strength has not been reached. The result is the spring losing strength or elasticity.
Creep can be demonstrated by hanging a weight on a rubber band and observing the change in length. If the weight is removed quickly, the rubber band will return to its original length, but if the weight is removed after an extended period, the rubber band will have a permanent increase in length after the weight is removed, which occurs because of creep.
The same situation will ensue with a spring. A Compression Spring will exhibit a reduction in free length, and an Extension Spring will have an increase in length.
If creep becomes excessive, the deformation in the spring will reduce the amount of available potential energy, and the spring may no longer function as intended in the application. At this point, the spring will need to be replaced. Creep can lead to spring failure if it goes unnoticed, which can be hazardous for the machinery and personnel.
How to Prevent Creep?
The variables that affect creep are stress, time, and temperature. Increases in any one of these will increase the amount of creep.
For most applications, reducing material stresses is generally the easiest means of mitigating creep. Some ways to reduce stress (assuming everything else is held constant in the design) include:
- Increase material thickness or wire diameter
- Use a larger spring to increase the outside diameter of the spring
- Reduce the percentage of the maximum of deflection on the spring
Additionally, the life of a spring can be extended with the same conditions or parameters with the following:
- Changing the material or alloy
- Special heat treatment processes
- Advanced surface finishing processes
ASRaymond offers a variety of materials, finishes, and testing capabilities that can aid in the reduction of stress creep. Visit the Manufacturing and Finishing page for a list of the standard offering. Contact Us to learn more about our capabilities and provide the right spring component for your application.
About ASRaymond
ASRaymond, a business of Barnes Group Inc, is a global leader in providing manufacturers with precision-engineered force and motion control solutions from world-renowned brands such as Raymond®, Industrial Gas Springs™, SPD™, and SPEC®. Servicing a wide range of industrial markets, including Construction and Agriculture, Lift Equipment, Marine, Medical, and Heavy-Duty Trucks, ASRaymond has the breadth and depth of standard products to match any application's demands. Additionally, ASRaymond's global team of engineers are available to customize components when standard products are not suitable. For more information, visit ASRaymond.com.